很多工厂所使用的维护策略都是简单的东拼西凑:持续运行直到出现故障的策略,或者定期的预防性校准,以及对故障频发的部件进行周期性故障诊断。
既然不能更新整个工厂的设备,那不防尝试一下基于工业物联网(IIoT)的策略,它适用于几乎所有的工厂,能够自动运行一个基于状态的程序来识别异常情况。
该策略利用无线连接,将手持式测试仪表连接到智能手机和云服务器上。无论是经理和管理层,还是工程师和技术人员,都可利用软件将数据导入到机器健康状态矩阵,再辅以相关分析工具,就可帮助用户实现预防性的维护。这种基于状态的程序也能帮助进行故障诊断和根本原因分析。
控制应用可从设备数据的基线和趋势分析中获益,包括变频器(VFD)以及相关的旋转设备(电机、泵等);控制回路;可编程自动控制器(PAC)和可编程逻辑控制器(PLC);以及气动元件等。
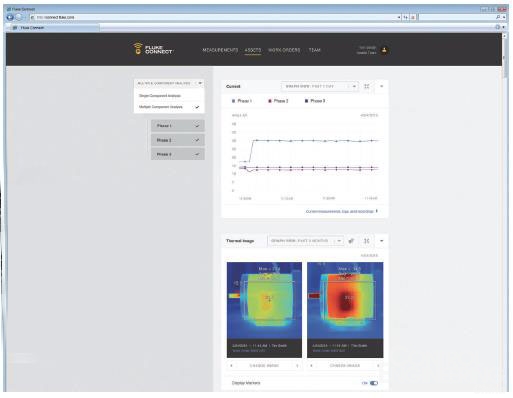
该屏幕显示的是喷涂在某个设备上的数据点,以及收集的数据点数据随时间的变化情况。图片来源:Fluke
大数据带来的挑战
工厂产生的大量数据对于很多传统制造企业来说是一个挑战,同时,大量本地存储的数据也可能会因计算机硬盘、火灾或其它方面的原因而产生丢失的风险。企业应该如何收集和分析这些数据,并将这些数据提供给所需要的人员?随着时间的推进,软件和数据存取技术也在不断的进步。
即使有了计算机维护管理系统,也很难利用所收集的电压、温度、电流和振动等技术参数的典型范围来做分析。要从上述数据中得出工厂所有资产的故障模式,是一个耗时巨大的工程。
例如,如果不能将某条关键生产线的PLC输入端出现的瞬时电压源隔离出去,可能会给出错误的信息,导致检修团队过度反应,甚至他们会建议更换整个装置,但其实只是其中一个元件出了问题。 没错,这仍然没有解决潜在的问题。
考虑采用先进技术、具有无线连接的测量工具,比如热成像仪、供电质量分析仪、数字万用表、手持式示波器、电阻测试仪,能够帮助帮助在生产线实现系统化的数据采集。采用先进的测量工具,有助于:
1. 在正常运行期间为关键设备创建参考基线;
2. 持续进行同样的测量,这样当故障发生时,数据可以被用于确定故障模式。

连接仪表与创建基线
指定专门团队,在基于网络的软件中,为单个设备创建测试点并编目。例如,在电机和靠近皮带、PLC电压输入输出、电机联轴器以及压缩机电源的位置涂色(热成像位置)。在软件中,将这些测试点与相应的设备关联。
让技术人员配备适合的测试仪表,包括振动表、红外线成像仪、电压或电流模块、手持式示波器、电源质量分析仪,以及可以对多个测试点和多个设备的数据进行组织、存储和分析的软件。
当生产线在正常模式下运行时,技术人员利用连接的测试仪器对每个测试点进行基准测试。测试按照逐条生产线进行。在初始的测试采样中,可以对运行在同一个应用中的多个相同的设备所得的数据进行平均,以便获得标准差。
技术人员将数据存储到特定的机器和测试点,然后利用智能手机自动将数据从测试仪表上传到云服务器中。(在某些情况下,工程师可能选择用电压模块或电源质量分析仪来记录一段时间内的测量数据。)通过app或基于网络的桌面软件,这些数据也可以实时共享给任何地方。
数据采集的要点
在同一位置采集数据的4个提示:
1. 每个测试点都和可在线识别的设备相连接,来自单个设备的数据被存储在基于云并经过加密的服务器上。
2. 在规定的时间点,技术人员分别在PLC上和连接的设备上对同样的点进行同样的测量;为了达到最好的比较效果,测量最好在一致、可重复的运行工况下进行(理想情况下是每天的同一时刻)。
3. 当生产线出现问题时,不仅要记录下被测对象的测量,还要记录可能会影响被测设备的其它设备的测量数据。
4. 在软件中,基于时间轴,使用分析仪表来比较测量结果和资产性能,利用所得信息制定更明智的预测性决策。
比较和分析
在进行分析时,需要注意以下3点:
●检查状态变化、阈值超限情况,检查状态从基线偏离情况;
●比较测量趋势,识别出任何异常工况,比如过电流或与系统压力相关的工况;
●使用软件功能来一一比较从不同技术获得的数据,将其与出现在PLC或相关设备上的特定事件关联起来。
同时,需要思考下面的问题:
●PLC输出电压波形是否发生畸变?
●红外线检查测试点是否显示出温度突变?
●电机拖动传送带时,振动水平是否增加了?
随着时间的积累,利用从多个测试仪表采集的带时标的数据创建矩阵,有助于发现系统故障的根本原因。不是查看单个设备的单个测量数据,而是将从多个设备上获得的多种类型的数据关联起来分析,还可与同一系统内的其它关键设备相比较。
无线测量与基于云的软件
基于云的软件和无线的测试工具,能够帮助用户:
●收集所有数据,避免因手动输入数据而导致错误;
●收集历史性能数据,建立有价值的性能基准。
●在同一屏幕上查看所有数据,避免管理多个软件。
●关联多个数据点,比如电压、电流和热成像,这样就可以快速发现异常工况。
●获得多个数据点和趋势图形,比较每个设备,有助于执行预测性维护计划,满足运行目标。
●实时获取现场资产设备状态的更新信息,因为技术人员可以使用移动电话,可以立即将设备的状态从正常改变成有风险。
●可以连续一贯的收集系统特性和支持信息,而不管值班的是谁。
经过长期的积累,将这些智能数据存放在一个便于访问的地方,只要有了访问权限,团队中的每个人都可以实时了解。通过基于工业物联网(IIoT)的测量解决方案,工厂经理可以更有效地收集和分析设备生命周期内的数据,从而及时排除设备异常和故障。(作者:Glenn Gardner)