对制造业数字化转型来说,很关键的一点是要通过虚拟化功能,创建仿真以及使用数字化模型,来将生产操作从工厂车间里模拟出来并形成制造优势。设计和组装部分必须扩大其作用并生产出两个产品,一个包括相关产品纯信息的虚拟模型,另一个是其实际物理对应物。数字化使我们能够做到这一点。
数字化生产制造赋予了操作人员灵活调整产量,以及在整个流程中较早交付多个产品型号的能力,这些都是实现项目收入最大化并最终实现利润最大化的关键因素。在初始阶段,可以在原型中心里对生产制造流程进行概念上的虚拟化,接下来在生产中心里转化为量产,从而在全球市场上提升其业务灵活性以及成本控制。
不仅如此,数字化生产制造为操作人员提供了自由交流设计知识和技术经验的机会。反过来,数字化生产制造也实现了对生产瓶颈的有效识别,这样工厂就可以通过对产出的优化调整来满足高峰时的需求。
在与一家领先的国际化软件公司的协作中,一家法国瓷器制造商通过将整个设计和开发流程迁移到云端,对其整个生产制造理念进行了变革。该平台的目标是不再进行成本高昂的物理原型制作,让制造商创建并验证可以为开发模具提供参考点的虚拟模型。该公司也准备对其现有的产品目录进行数字化,以保留其150年的设计贡献。
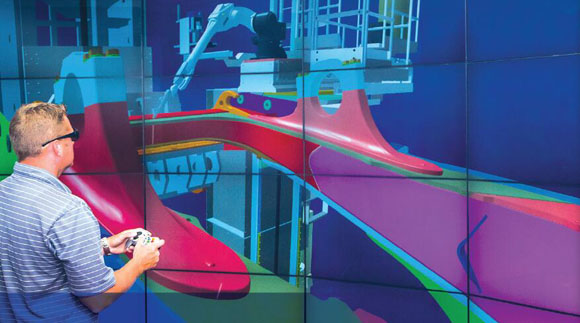
虚拟产品原型技术以3D线框图技术而著称,该技术与乔治·卢卡斯在1977年的电影“星球大战”中创造死星时所用的技术一样。工程设计人员进一步利用了该流程,使用扫描样本来对虚拟模型进行分层,以此识别出制造产品所需要的合适的材料。
随着可持续性已经变成了至关重要的性能指标,测试及选择材料的过程需要进行简化。因此,虚拟原型设计需要在节省宝贵的资源的同时改善可持续性。
以数据为驱动力的方式
在原型开发阶段之后,生产制造商就要努力满足在第一批产品中实现设计及功能性的重复性。目前,这需要对有争议的精度问题进行昂贵的实体质量检查。
从工程设计的角度来看,解决这些特定的挑战需要一个以数据为驱动力的方式。生产制造流程需要在数据产生的过程中对其进行捕捉,同时制作出一个反映实体产品的镜像虚拟模型。这为实现产品规范管理(PSM)系统奠定了基础。
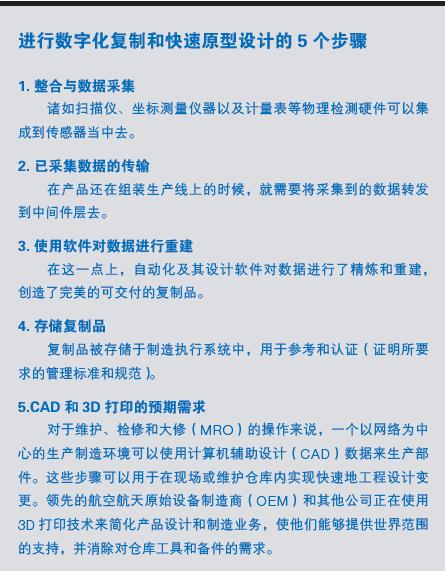
制造生态系统
这个想法是努力构建一个制造生态系统,能够在空间、陆地或海上按需创建组件和工具。目前,激光成型技术以及数字化设计数据正在用于将粉末材料合成为复杂的航空电子结构件,如F/A-18E/F导管。在一种称为选择性激光烧结的工艺中,使用钛金属和其他材料打印出不同大小的部件。
虚拟化制造的应用正在不断深化。当一家企业使用物理原型来进行设计迭代的时候,某些材料类型(诸如金属)不能以理想的成本来进行数字化制造或机加工。如果最终产品的材料和原型的材料不同,即使公司采用了快速成型或3D打印技术,也无法准确预测最终产品的材料属性。
当涉及到结构设计的时候,无论是茶杯,还是飞机和汽车都需要面对同样的挑战。材料的选择、耐用性以及设计的灵活性,都需要和产品在现实世界中与力、热以及震动的相互作用保持一致。在这种情况下,虚拟化制造可以将有限元分析法(FEA)提升到另一个层次。例如,焊接模拟(涉及到热应力和残余应力相关因素)会有助于优化工具设计以及实际的焊接工艺。研发工作正在积极为自动化流程优化的模拟和预测开发FEA软件。一旦与控制系统整合起来,它将可以在工厂车间里对工具进行再次校准,在不需要人工干预的情况下完成对设计、工具、制作以及材料的变更。
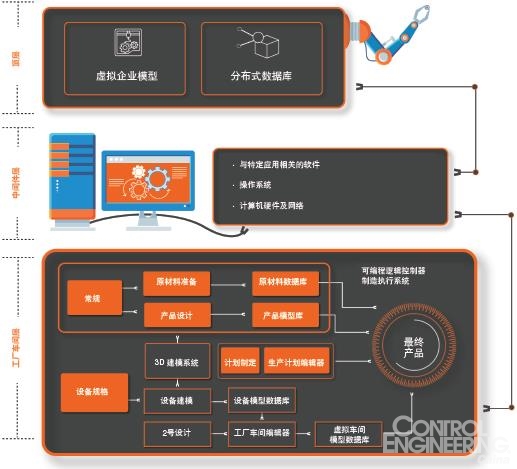
虽然虚拟制造开始作为设计和测试工具的一种方式,但它已经发展成为支持生产过程乃至产品开发的强大力量。通过数字模型可以捕获产品信息,以便在工厂车间进行快速原型设计并最终实现批量生产。图片来源:L&T科技服务公司
数字化双胞胎
生产制造业的未来要依赖于使用虚拟产品信息来提高产品质量。在现实中,通过使用来自于整个生产生态系统的合并数据,我们几乎已经将整个工厂车间都复制下来了,创造出了数字化双胞胎。一些先进的科技企业已经开始探索此概念了,例如创建风力发电场的工作模拟软件来预测设备的故障并且提高日发电量多达20%。
虚拟调试可以让操作员通过创建一个虚拟工厂,并将其与真实的控制器连接起来,以全面地验证一套生产制造系统的可持续性。这需要完整描述工厂的仿真模型,详细到传感器和执行机构的层面。通过将模型与真实的控制器连在一起,工程师可以在实际的调试阶段还远远没有开始之前就检测到控制程序的潜在错误。
一个模拟的工厂车间可以监控各项参数、暴露出生产的缺口、凸显成本利用的低效、减少碳排放量。相同的概念和原理也可以应用到产品上面,即使它还在画图板上也可以了解到未来在现实的世界中是如何工作的。(作者:Mayank Pandya)