半导体公司谨慎地管理着他们的半导体晶圆片生产线 (“晶圆厂”),旨在实现正常运行时间、良率和生产量的最大化。工厂运营团队不断地寻找新的方法以从制造工艺中“挤出”哪怕是百分之零点几的效率升幅。
在硅谷晶圆厂里的晶圆片制造工艺中,使用了超过 175 个特种气体钢瓶。必须密切地监测这些气体钢瓶以确保不间断的气体供应。一次意外的供气中断将导致价值数十万美元的晶圆报废、收入损失和在产品发运给客户的过程中出现不可接受的延误。为避免停机,技术人员一天三次手动地记录晶圆厂中每个气体钢瓶的压力。但该手动过程容易出现人为错误,而且维护成本高昂。
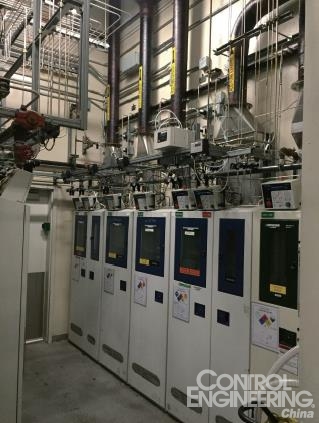
■ 半导体制造设备中的气体燃料仓,无线节点必须在到处都有的金属和重混凝土构造物中间可靠地运行。
此项工作通常以手动方式完成是因为在晶圆厂中进行通信布线是昂贵和不切实际的。气体钢瓶遍布整个工厂,而且对于大多数钢瓶而言其附近并没有 AC 插座或以太网插口。出于安全原因建筑物是由混凝土墙搭建的,因而使得安装新的电线成本太高。此外,安装电力线和通信线的大型建设项目还将扰乱生产流程,从而导致工厂停工。
这家半导体公司采用的解决方案是,部署一个含有 32 个节点的SmartMesh IP无线网格网络,以监测气体燃料仓中的气体压力。每个节点由一对 AA L91 锂电池供电 (电池寿命约为 8 年),因此安装该网络不需要进行额外的布线,而且没有不必要的停机。尽管面对着晶圆厂中的混凝土构造物和普遍存在的金属结构,但是此网络仍然证明自身是极其可靠的。到撰写本文的时候为止,该网络已经连续正常运行了 83 天以上,并以>99.99999% 的可靠性传输了超过 2,600 万个数据读数,这比人们对于高可用性通信和计算机系统所期望的严格可靠性水平更高。
在气体燃料仓中,测量每个钢瓶的罐体压力和调节压力,并通过SmartMesh网络把这些读数传送至一个中央监测系统。每个SmartMesh节点连接至一对钢瓶,并通过无线网格网络把数据发送至一个覆盖整个建筑物的网络服务器。在控制室里,晶圆厂的站点管理软件工具显示实时读数并计算运行率,以建立针对钢瓶更换的常规时间表 。此外,还设定了低压力门限,以在钢瓶早于更换时间表的进度安排便达到了低压力水平时向设备技术人员发出警示。警示信息显示在控制室监视器上,并以“全天整周”的方式通过互联网传递消息。
通过使用实时气体消耗率,技术人员能够精准地预测气体钢瓶什么时候将需要更换,从而减少由于过早更换钢瓶所导致的未用气体浪费。在日常运营中其好处可扩展到提升效率以外。集中收集气体使用数据并使工厂管理层容易获得数据,该系统可提供趋势分析,通过使读数与特定的半导体晶圆工艺和几何尺寸相关联,可进一步确定机会以简化工厂运营。这有助于在需求量攀升时优化晶圆厂的产能增长。
对于半导体晶圆片设备而言,优化正常运行时间及提高作业效率将导致生产量的增加。安装必须是非破坏性的,适合现有的空间范围,并且在金属和混凝土结构中可靠地工作。
在硅谷半导体晶圆片工厂里安装了一个SmartMesh IP 无线网格网络以简化制造作业,监视气体钢瓶使用情况并把实时读数转发至工厂管理软件。该数据可实现快速和准确的气体使用量估测,确保及时地进行气体补给,从而减少停机时间和气体的浪费。记录数据点并将其用于帮助进行产能的计划。
凌力尔特的Dust Networks产品是连同无线网格网络软件的芯片和预认证 PCB 模块。当嵌入到客户的传感器和网关产品中时,形成的无线连接可实现>99.999% 的数据可靠性和超低功耗,从而使传感器可以安放在严苛的工业物联网 (IoT) 环境中。Dust Networks的产品经过现场验证,已在 120 个国家部署了超过 50,000 个客户网络。(本文作者:Ross Yu,Dust Networks 产品市场经理;Enrique Aceves,远程办公室设备经理。)