两化融合是信息化和工业化的高层次的深度结合,是指以信息化带动工业化、以工业化促进信息化,走新型工业化道路;两化融合的核心就是信息化支撑,追求可持续发展模式。在制造业企业中,迫切需要一个整体解决方案——用以解决多部门之间的协同问题。本文着重介绍将3D/2D数据,通过PDM系统,贯穿制造业企业的设计及制造的整个过程。
1 智能制造解决方案
智能制造源于人工智能的研究。一般认为智能是知识和智力的总和,前者是智能的基础,后者是指获取和运用知识求解的能力。智能制造应当包含智能制造技术和智能制造系统。本文重点介绍智能制造系统中的整合应用。多系统整合过程详见图1。
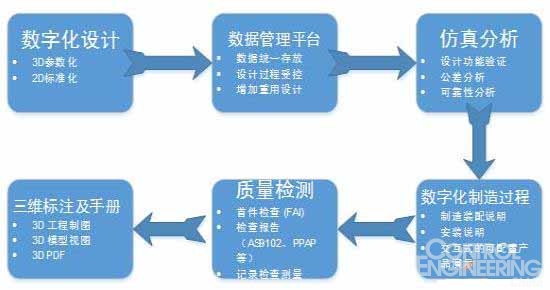
图1 多系统整合过程
2 数字化设计
易于使用的强大3D CAD设计功能为直观的产品开发解决方案提供了支持。快速创建、验证、交流和管理产品开发过程。将产品更快投放市场,降低制造成本,并提高各个行业和应用领域的产品质量和可靠性。
2.1 3D参数化
使用3D设计软件中的3D实体建模功能,加快设计速度,节省时间和开发成本,并提高生产效率。3D实体建模是现代化产品开发的关键方面,为设计、仿真和制造跨各个行业、应用领域和产品的任何零件和装配体提供了基础。
3D实体建模可以加快复杂零件和大型装配体的创建速度。为设计创建3D实体模型而非2D工程图:
●加快设计开发和出详图的速度。
●改进直观显示和交流。
●消除设计干涉问题。
●检查设计功能和性能(无需物理样机)。
2.2 2D标准化
利用2D工程图自动更新功能,您不必担心修改问题。所有2D工程视图都从3D实体模型自动创建,并自动链接到3D实体模型。如果修改了3D实体模型,2D工程视图和细节会自动更新。这种自动关联性意味着实体模型始终与2D文档保持同步。
3 数据管理
PDM产品数据管理解决方案来管理所有类型的产品开发文件。强大的文件管理解决方案可提供所需的集中式文件入库功能来管理和控制电子知识产权和产品设计数据。
3.1 数据统一存储
借助PDM创建并维护可供存储和检索文件的单个数据位置和库。除了保留产品设计数据的安全备份之外,安全文件入库还可让您消除多重信息“孤岛”、重复文件和不同步的修订。
3.2 自动执行业务流程
PDM的直观图形用户界面可规划工作流程并最大限度减少管理工作,同时自动跟踪审批和签字并保持其准确性和责任落实。
●利用多个工作流程处理不同文档类型和审批流程。
●通过并行过渡帮助多个需求审批人员。
●利用序列号生成器自动创建并分配属性,如零件号、项目编号和文档ID。
●自动创建项目文件夹结构和标准文档,从而有助于确保数据的一致性和完整性。
3.3 文件参考引用管理
管理文件参考引用(零件、装配体和工程图之间的链接)同管理文件以保持产品开发数据完整性一样重要。PDM系统可管理所有文件参考引用,并在将文件移动到不同文件夹或重命名文件时自动更新这些参考引用,从而消除断开的参考引用和避免花时间手动查找和修复丢失的参考引用。
4 仿真分析
使用CAE的强大工具有效地评估设计中的非线性和动态响应、动态载荷和复合材料强度等。CAE工具可以提供有价值的洞察,从而以最经济有效的方式提高产品可靠性,无论是什么材料或使用环境。
4.1 热结构分析概述
热结构分析是用于计算固体结构中温度分布的有限元方法应用,而温度分布是由于设计中的热输入(热载荷)、输出(热损失)和热障碍(热接触阻抗)造成的。热结构分析通过仿真计算热传导、对流和辐射,解决共轭热传导问题。
在热结构分析中,应用两种传热方法(对流和辐射)作为边界条件。对流(由表面薄膜系数设置)和辐射(表面发射率)都可以与环境交换热能,但只有辐射能够在装配体中不相连接的实体之间传递热能。
4.2 振动分析概述
产品可能遇到的振动会降低性能,缩短产品寿命,甚至导致完全失效。振动效应在您的产品上是随时间变化的载荷或者瞬态载荷,很难预测。
●振动载荷可能会在结构中激发动态响应,导致高动态应力。
●忽略动态应力会导致您假定的产品或结构的安全系数(FoS)高于其实际情况。
4.3 有限元分析(FEA)概述
使用有限元方法的位移公式在内部和外部载荷下计算零部件的位移、应变和应力。通过使用四面体单元(3D)、三角形单元(2D)和横梁单元来离散被分析的几何体,并通过直接稀疏求解器或迭代求解器对其进行解算。同时提供了针对平面应力、平面应变、拉伸和轴对称选项的2D简化假设。有限元分析可使用h或p自适应单元类型,该自适应方法可确保解算会收敛,这将为设计师和工程师带来巨大优势。
对于壳体网格划分,有限元分析提供了一个效率工具来管理零件或装配体文档的多壳体定义。它将工作流程改进为根据类型、厚度或材料来组织壳体,并允许更好地可视化和验证壳体属性。
由于大多数工业零部件都是由金属制成的,因此大多数FEA计算涉及金属零部件。对金属零部件的分析可由线性或非线性应力分析执行。使用的分析方法取决于设计达到的高度:
●如果您想确保几何体保持在线弹性范围内(即,载荷一旦消除,组件将恢复到其原始形状),那么只要相对几何体而言旋转和位移较小,您就可以考虑采用线性应力分析。对于此类分析,通常将安全系数(FoS)作为设计目标。
●在评估后屈服载荷循环对几何体产生的效应时,应执行非线性应力分析。在这种情况下,应变硬化对残余应力和永久变形(变形)产生的影响应该是关注的重点。
5 数字化制造过程
数字图形化内容支持各种用于制造、服务和培训的技术交流应用,其所要达到的目的在于:
●发布清楚、详细的2D和3D说明,准确展示装配车间的复杂操作。
●使用3D可视内容发布用户说明。
●为机床操作员和维护工程师创建维护、修理指南。
●以印刷物方式或在线提供3D零件目录,争取客户订单。
●为QA工程师开发形象化的测试步骤手册。
直观的技术交流:
●使用视觉3D交流材料而非文本与非技术受众或讲其他语言的人员接洽。
●创建易于理解的清楚且直观的3D视觉内容。
●使用交互式动画和3D可配置交流材料,创建更加丰富的产品体验。
●即使在产品制造之前,也可以使用图形3D交流材料展示产品的装配、修复或操作。
6 质量检测
公司质量部门肩负着执行质量检查流程的任务。这通常涉及创建文档,例如带有零件序号标注的工程图、供在检查过程中使用的报告或零件所需的其他交付内容。这项耗时的工作通常是设计师、工程师和质量检查员的责任,他们可能每天花费大量时间手动创建所有这些文档,并且不得不在电子表格中手工输入数百个特性、尺寸、公差和注释。此外,这一冗长的过程容易导致人工抄写错误,这在一段时间后可能造成严重损失,甚至危及您的质量承诺和认证。工程师或客户对模型所做的任何更改都可能导致工程图修订,这要求质量检查员重做工作并重新输入所有特性。许多企业要求工程图上零件序号的创建以及检查数据表和报告的创建均实现自动化,从而简化检查流程。自动应用按顺序编号的零件序号,以帮助跟踪要检查的尺寸和特性。
其参数化的图纸可参照图2定义,零件检查表可参照图3样式布局。
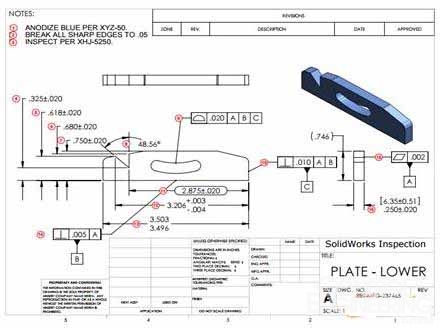
图2 参数化的图纸

图3 零件检查表
7 三维标注及手册
7.1 清晰的结构化3D演示
除了3D PMI定义之外,利用不同的视图和显示设置将丰富的数据融入清晰的结构化3D演示中。甚至可在您旋转模型时智能显示和隐藏3D注解,以便在尊重所有关键功能注解时增加清晰度。
7.2 自定义3D输出模板
通过自定义3D输出模板为多种交付物和部门提供服务。您可以构建布局、插入公司或集团徽标、放置3D视口和缩略图、编辑文字说明、内嵌元属性链接和添加表格。一旦设置这些模板,它们就将作为所有部门(例如制造、运营、QA和采购部门)在多种交付物(如工程图、请求报价(RFQ)、检验报告和工作说明)方面的内部和外部过程指南。
8 结论
中国制造2025已然发布,今后的制造业将两极分化,设计创新型企业的利润率将持续走高,而附加值较低的低端制造业将被逐步淘汰。对于制造业企业而言,应借助相应的信息化工具,用以帮助企业将更多的精力投入到设计研发及精益制造过程中。