加工制造工艺和生产智能化已经受益于科技的快速进步,安全方面亦是如此。回顾历史,在生产设备内部或周围保护工人的最常见的方法是在工人和运行的设备之间设置实体围栏。
尽管这样类型的安全系统可以带来安全生产并满足相关的规定要求,可是它限制了生产能力并且可能需要大量的维护工作。如今,已经有了不需要实体围栏的技术,而且即使说不能提供更好的安全,至少可以提供相同水平的安全。
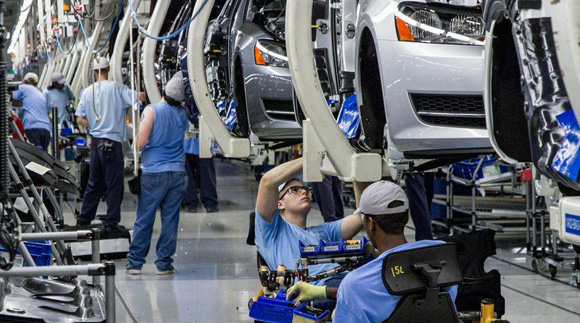
评估安全风险
现代的安全技术展示了显著增加产能而同时不会牺牲可靠性的好机会。这是关于开放生产线以及提供更好的设备操作及可视性的问题。光幕、激光扫描仪以及区域(3D)扫描器可以集成到现有的设备中。除此以外,诸如协作式机器人这样的一些设备也已经集成了安全特性。
那么,你该如何开始呢?首先进行安全评估。先开始审核现有的生产线,识别已经出现的风险,并制定出保护人员远离风险的可行性措施。
作为评估的一部分,为工厂里的每一个操作指定风险类别,考虑其潜在伤害发生的严重程度和发生的可能性,以及其他的因素。这将决定该操作所需的防护级别。这一评估过程将公司现有的安全缺陷展露无疑。 您的当务之急应该是尽快解决这些缺陷,因为这些是公司的潜在责任。
下一步,识别出风险来源、估算风险、评价风险、以及确定其是否是可接受的还是需要消除的。使用风险树可以为下列的每个参数进行评估:伤害严重程度、暴露于危害的频率、以及避免危害的可能性。这是一个经过考验过的用于管理人和机器的架构,拥有这样的架构对于安全来说至关重要。最终,安全从设计及工程部门开始,继而覆盖到生产和管理部门。
机器人安全已经得到了显著的提高。3D视觉和工业计算机一起创造了为工作环境下的机器人、车辆、起重机或升降设备规避碰撞而进行实时计算的能力。在光学和软件方面的进步以及新的安全文化会继续推动机器人应用于新的工业领域,这些产业因此会收获灵活性、安全性以及机器人带来的工作协作等好处。
人机协作的安全性
未来,更大型的、更快速的机器人会与工人们安全地协作。通过从视觉系统获得的诸如3D激光扫描仪或光的成像、感应以及测距(激光定位器)、以及后台运行的代码等输入信息,机器人的安全性将大为提升。
工作人员可以走进工作区域而不需要执行挂牌上锁流程或者强制机器人完全停下来。取而代之,机器人会慢下来或者根据传感器和软件的反馈调整其路径。这种动态的碰撞规避环境可以在减少总的设备停机时间的同时,确保产品、机械设备和人员的安全。近些年来的自动化展会上已经流行这样的展示了。科技在进步,安全也在改善。
通常来说,当人们谈论机器人协作时,他们专注于机器人技术,忽略了机器人在其工作环境中以及有人的情况下如何工作。 目前,主要有4种类型的协作操作:
1.安全级监控停止,允许让操作员在机器人停止的时候与其交互,当人员离开协作工作区时恢复自动运行。
2.手势控制操作,允许操作员使用手部控制与机器人直接接触。
3.速度和分区监控,通过定义不同的安全区域,让机器人的速度根据区域不同而改变。当操作员出现在可能碰撞的区域时,会发出保护性停机。
4.功率和力量限制,在机器人与人员之间发生偶然碰撞时,力量限制功能使之不会对人造成伤害。
速度和分区监控可以让机器人感应到操作员的存在并调整其速度。通常来说,这种方式是通过使用安全传感器应用到无围栏的机器人上。通过使用激光或视觉系统可以在碰撞发生之前进行预测,系统已经创建出了多个工作区间。
这种方式可以让机器人在附近有操作员的情况下继续工作,因为机器人的特定的速度已经是由预设定的安全区域所决定的。如果操作员过于接近,机器人会停下来。这样的动态碰撞防范是机器人可以对其所在环境变化做出反应以及增加灵活性和实用性的底线。
机器人不会与机器设备的主体或者一小块发生碰撞,这一直都是至关重要的。近期的一个项目通过使用速度和分区监控实现了这一点。操作员可以通过人机界面(HMI)观察机器人的运动。如果机器人安全运行,它在屏幕上为绿色。当机器人进入警告区域时,颜色变为黄色,机器人同时会减速。如果机器人进入碰撞区域,它会变成红色并停止运行。
随着科技的功能和复杂性不断增加,将工业安全优先考虑正在变得越来越重要。系统集成商可以发现不安全的状况并帮助企业解决风险。风险评估和修正措施帮助企业避免不必要的安全事故,并带来显著地投资回报。
正确的安全策略,不仅可以为企业提供更高的安全可靠性,提高生产率,最重要的是,还能最大限度地减少因不安全操作造成的计划外成本,以及由此造成的人身伤害。(作者:Michael Lindley)